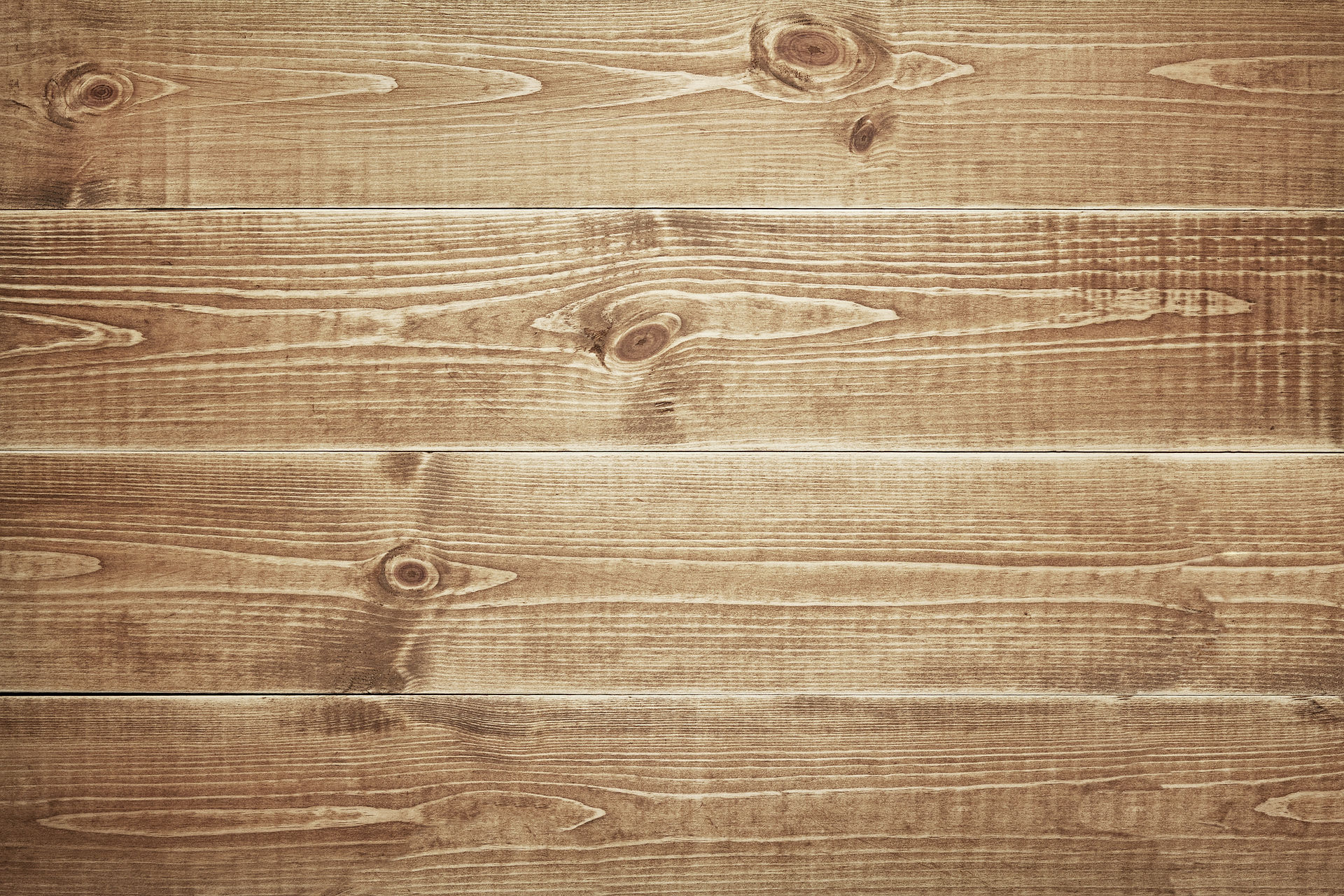
The Zinc roof......bring on the professionals!
After deciding to use Zinc at the design stage, we had been checking out websites, looking at buildings referred to us by different contacts and so on. We had received quotes from out of area companies more used to this type of work, but their price included for accommodation to stay whilst doing the work, and we felt that to keep costs down we really needed to use somebody local. We did find a couple of businesses willing to undertake the work, one of which sent photo's of some recent Zinc work they had carried out in Truro. In truth I would not have sent those pictures out, they actually put us off! In the case of W H Joce, now Joce Roofing, their website indicated that this was their forte. I spoke to the owner, Bill Joce, and after receiving their quote we took them on. Work commenced on 29th November with Lee and Wayne arriving first thing.


I hadn't quite finished all the soffits, but I was in a position to keep ahead of them and out of their way. I also had to fit some stainless steel bug mesh to enclose the ventilation space under the decking. This type of roof is referred to as a 'cold' roof. The Tyvek membrane over the rafters/roof joists encloses the insulation and therefore retains heat, within the roof space. There is then a 50mm space, battened off, with the 22mm ply on top. This ensures that the Zinc is ambient both sides and does not sweat, and suffer from condensation that would arise if one side was warm. The mesh is there to allow air circulation whilst preventing insects from finding a new home for themselves.
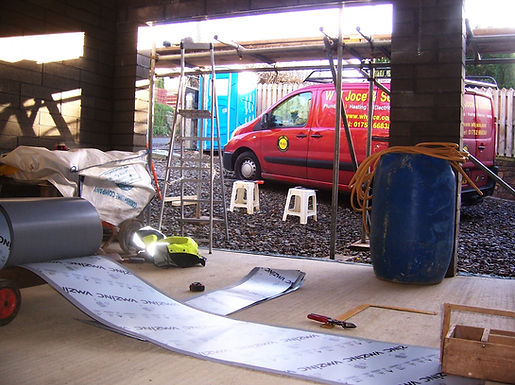
With most things in construction, you would have some idea how something is done, but I could not even imagine how one would actually go about fitting a metal roof, so the whole process was very interesting to me. Apart from screws nails and clips, everything is made from the rolled Zinc, we had chosen Quartz-Zinc, which has a pre-patinated finish that will not change significantly, and it is said has the look that natural Zinc will eventually achieve. Lee said that this was the type used in most of the work he undertook. They had bought along a shearing machine, and used this to cut the thin strips that they used for the preparatory work.
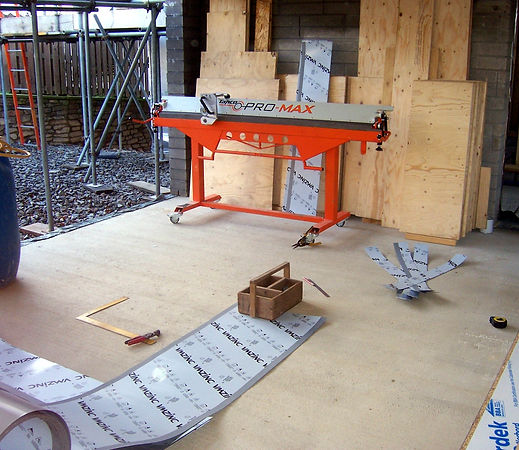
The first strips were nailed along the edges of the fascias and barges. The fascias would be made to hook around these and fixed out of view above. This was another aspect of this method that made it appealing, no fascia boards to paint...ever.

Next came the fascia, fitted in sections with each one interlocking and watertight, no sharp edges left. On the vented faces, strips of Zinc were cut and folded as shown in the picture right, and positioned to provide a clear flow of air under the roof deck. The roof panel ends would later be folded around the end of the projection to create a seal and a drip bar.

On the non-vented barges, the fascia strips extended above the deck height, and would later be folded down over the standing seams of the roof panels as shown above. It took a few days to complete this work around both house and garage roofs. Lee had brought along a folding machine to produce the long roof panels. The roll of Zinc was placed on one side, and was fed through a set of rollers to create the standing seams, it was amazing how rigid this made each panel.



The full set of panels was produced for each section of roof and carefully passed up onto the scaffolding, where they were tied down. It was getting quite windy, and it wouldn't have taken much for them to take-off. The panels were laid on a layer of Vent 3' membrane, and fastened with special stainless steel clips, solid through the centre section, and flexing for the remainder to allow for expansion of the metal as shown in the inset.


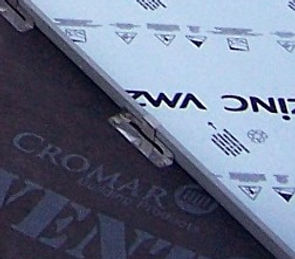
Over the next few days the roof went down without any issues. It was very cold at times now being in December, and it is easy to understand how difficult it was working with cold metal, Lee said it was almost as bad in the summer when the metal was hot!
As all the outer walls had a 50mm space for ventilation, where the lower roof met the wall to the upper roof, that space under the deck had to continue upwards.
I don't know whether you call it soldering or brazing, but Lee very neatly created bespoke solutions for each situation. In the case of the corner in the picture to the left, a separate flashing piece would also be fitted later to fit over the upstand and under the cladding to create a weathertight transition, whilst allowing air to flow through.

As each section of roof was completed, I installed the guttering. I had chosen the Lindab metal system in 'Dark Grey' colour, we felt that its chunky style suited the house well, and although not a colour match for the Zinc, or the doors and windows, we think it is a good blend. Lee suggested as the gutters were large and high capacity, we fit them level to give a better appearance, and rely on gravity to allow the water to flow out. When all Lee and Waynes work was finished, only then did they peel off the protective film. I thought it might have been a good idea to leave it on until the last minute, but Lee said that now that it was exposed, it would be a devil to remove at a later date.
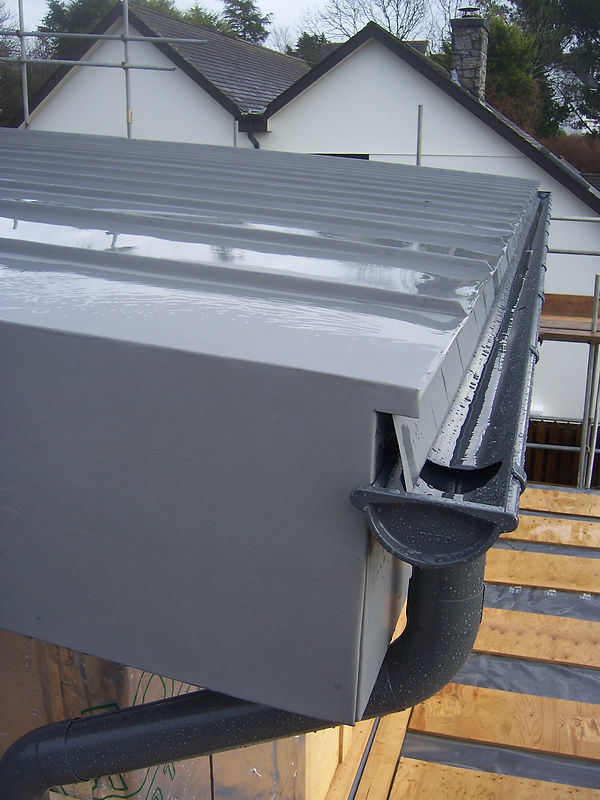

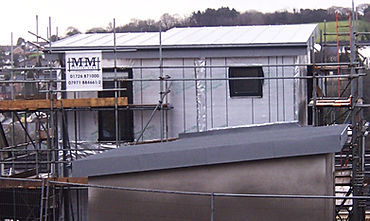

From start to finish, it took Lee and Wayne only 10 days to complete the roof, we did not have one problem, we were completely satisfied with the work we had done, and absolutely love the finished 'look'.
This type of roof does not come cheap, at around £16.5k it was quite an investment, and substantially more expensive than most roofing types. Nevertheless we felt, and still feel that it was worth the expense. You can hear heavy rain in the upstairs rooms, but it is not loud or oppressive, and we can relax in the knowledge that our investment will keep us dry and be maintenance free for many years.