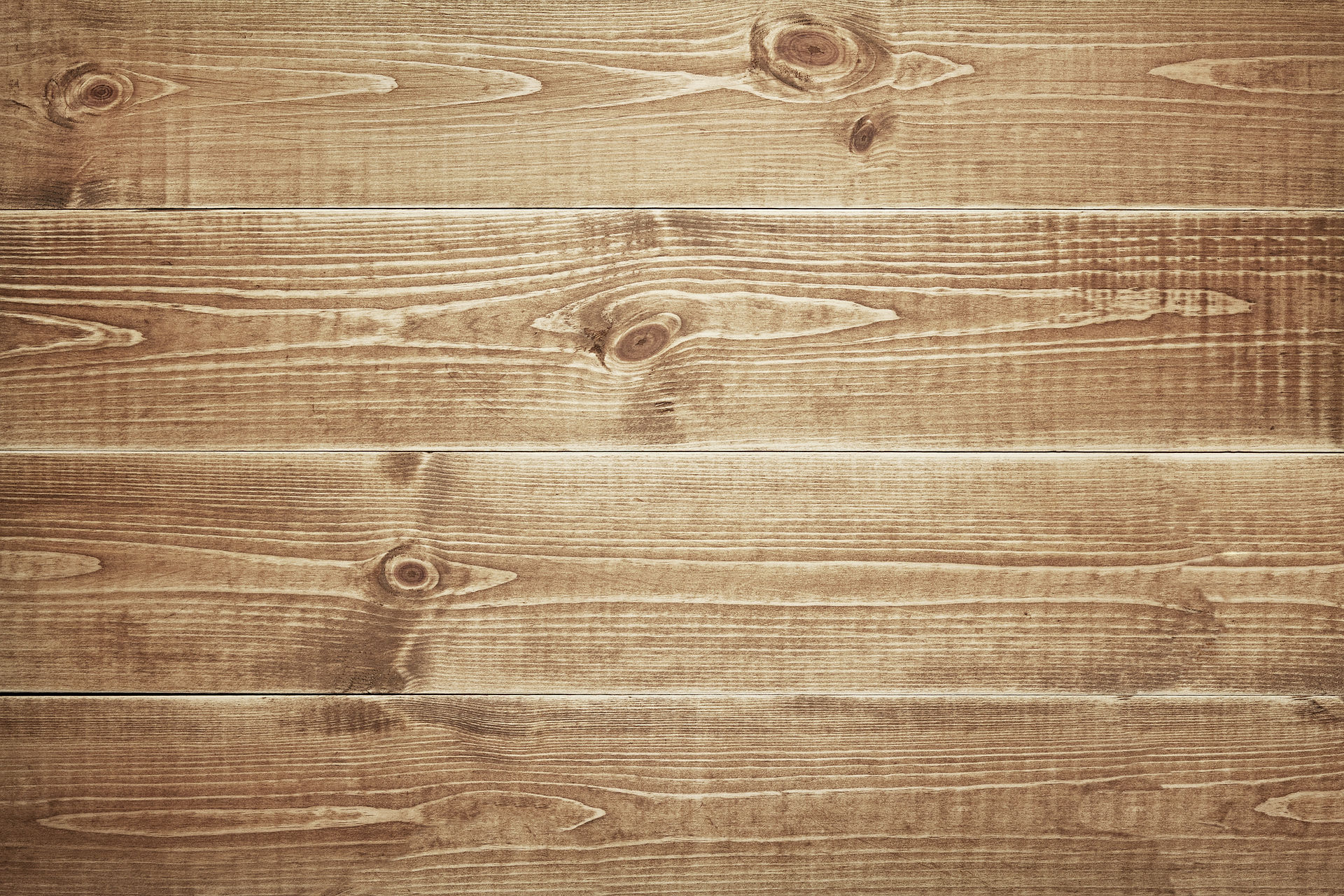
The Timber Frame goes up.......but not without its problems!
Over the previous couple of years, we had been mulling over who we were going to use to supply the timber frame, and to what level of thermal efficiency we were going to aim for. We never considered constructing a frame from scratch on site, as we thought that defeated the object, that being the assumption that panels would be accurately constructed in the dry and controlled environment of a factory, delivered to site as required and erected quickly (also hopefully in the dry). We had done the usual visits to Self Build Shows, including the National Self Build and Renovation centre in Swindon (which is well worth a visit), had talked to many a supplier and received a number of quotes, but our Architect was very keen for us to use Frame UK in Redruth. We got on very well with their Development Manager, Jane Stevens, who was always very helpful, and showed us around their very professional looking organisation; after an initial quotation, we decided that we would employ them to deliver the timber frame, and on 8th September paid the initial deposit to begin the frame design. In truth, pretty much everything about the way they did business was professional, it was just a couple of factors that eventually conspired to make the overall experience quite an unpleasant one...anyway a bit on that later...I digress. Once we were in a position to make real decisions, we had a number of meetings to ensure that Chris's design and the amendments we had made, together with any changes required as a result of frame engineering limitations, were understood and incorporated.

Although this is written following on from the section on groundworks, much of these discussions and work on the frame design was happening up to the point where we were waiting to commence work on the footings. The structural loading of the frame would determine the shape and structure of what was beneath it, and Chris had appointed Lee Barton (LB Structures) to produce the calculations and plan to allow us to commence with the footings. Frame UK also employed Structural Engineers to provide structural calculations for the designing of the frame itself, though this was included in the overall price, and the details were only given to us at handover. During September, as the frame drawings were being finalised, some adjustments were still being made to internal door widths, now all at 830mm, the height of the folding doors (to ensure thresholds were in a sensible position and not creating a trip hazard), and the inclusion of a 'loft' in the stairwell to house the MHRV system fan unit. As we had to order windows and external doors 3 months ahead, it was also vital that the apertures were 100% correct.

There are alternative types of floor joists that we could have used, solid wood, glue-laminated 'i' beams, and metal web posi-joists. We were advised to use posi-joists, made in house by Frame UK, on the basis of rigidity, lightness and strength, and as we were going to be threading ventilation pipes under floors, these were by far the best solution. However even these tend to have a fair bit of give in them over a large span. In the event, the first floor and roof construction would consist of 252mm depth posi-joists, delivered in cassette form, with peel-clean chipboard on the floor sections, and Tyvec on the roof sections (later to be decked with 22mm ply over battens and a ventilation space). Whilst we continued on with the groundworks, the delivery date for the first sets of panels was agreed for October 31st.

Having decided on a 140mm closed panel specification, there were options for increased thermal efficiency, each improvement having increased cost implications. The optimal point for us in terms of thermal efficiency and cost was their type 'D' 0.19W/M2K construction, which was well in advance of the then current Building Regulation requirements, but at code 4, still considerably shy of what can be achieved at a cost. Even so, this increased the price beyond the original quote, but we felt that thermal efficiency was the best way to achieve our aim to have a warm, comfortable home with low running costs. The diagram (left) illustrates the method, but we would not be building a masonry outer skin, which has no thermal benefit in any case. After cladding or rendering, and plastering internally, the total wall thickness inside to out would be 265mm.
All changes were quickly drawn up and sent to us for approval by Stuart Covill and his team at Frame. They were very approachable and willing to help throughout our association with them.
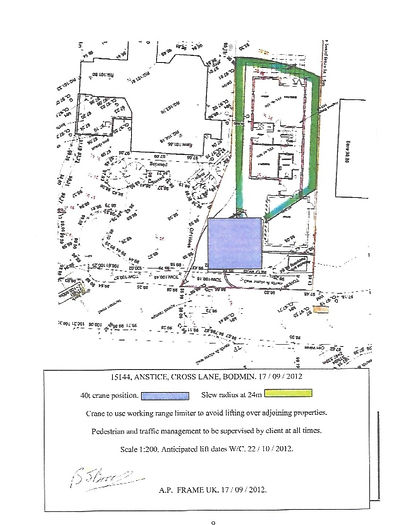
At this point, I was the only one on site, Shane and Tony having nothing to do for the moment. I had been provided with a 'lifting plan by Frame UK, and we were satisfied that we could accommodate the crane on site, having a little more than the 7mx7m indicated on the plan. The cost of the crane was included in the package, as we had opted for 'supply and fix', which provided for a machine with a capacity of 40 tonnes. On Tuesday 30th, I arrived to find a guy on site who introduced himself as Cameron, the Contracts Manager for Macsalvors Crane Hire, who had been appointed by Frame UK to carry out the lifting. He seemed most concerned, and told me that the crane that was arranged could not be used, as the slope within the 7x7 area available was too great. It would mean that the main load bearing outrigger would be packed up on well over 1 metre high of supports, and would not meet safety requirements. Why this had not been picked up or been mentioned previously remains a mystery, but I asked him what our options were. He told me that we could knock down the garage (aaarrgh!), or alternatively use a larger capacity crane to reach from the road, but we would need to apply for a road closure notice (AARRGH!!!). As neither of these options was good looking enough for me to consider, I asked him to put his thinking cap on again. To get the crane half on to the plot and therefore only partly blocking the road, he suggested bringing in hardcore to build up the area between the garage and the road, compacting it, and using spreading blocks on top to distribute the load. As we did not want to delay the frame delivery that was planned for the following day, this significantly less unattractive solution was suggested to Frame UK. We would argue about the cost of hiring and delivering speaders, and the larger 50 tonne capacity crane, at a later date.
Frame UK agreed this was our best solution, and I quickly rang Cherry Stephens at the quarry to ask if there was any possibility of their arranging to have a load of quarry waste delivered at short notice. They had someone with a wagon waiting in their yard at the time and we had it tipped on site within half an hour. I called Colin Bilkey, and he arranged for Gary to call in on his way home from a job later that afternoon to level it out and compress it. We were deeply indebted to Cherry, Colin and Gary yet again, and by the skin of our teeth were ready for the kick-off in the morning.
Also during the day, a small pick-up had arrived from Frame UK carrying lengths of timber for the sole plates, and ancillary construction materials. I had previously met the Frame UK Project Leader, Brian Young, who would be our main point of contact and oversee the timber erection right through to handover, he arrived to check out the site, and was joined by the erectors. Now apparently FHUK do not employ their own teams, they subcontract each build to a team of erectors who have their own negotiated price for the job. I was advised that our allotted team 'CKR Erectors', were one of the best, and this was my first acquaintance with them. This arrangement is quite possibly all fine and dandy when things go well, but pretty disastrous when things go wrong, as we were to find out pretty soon.

Their main man, Charlie if my memory serves me right (because I've long been trying to forget them all!), told me that CKR stood for Charles Righton, with the K for a middle name I can't recall. Personally I liked all four of the guys, but by the time their job was finished, I was extremely glad to wave 'farewell'! Anyway, they spent the afternoon laying DPC and sole plates held in place with masonry fasteners shot-fired into the blockwork.
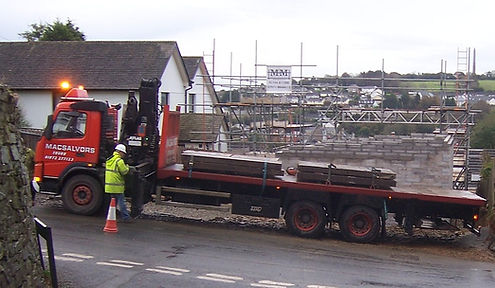
At 9.00 am on 'Build Day 1', Macsalvors arrived with 'Ekki' mats and the 50 tonne six wheel (all steering) crane. The truck arrived shortly after with the first panels and other component timber and steels. I have to admit that we were all pretty excited by so much sudden activity. Brian reckoned it would take a little over one week to complete, dependent upon weather conditions, tomorrow being November 1st, we would have to take what came along.


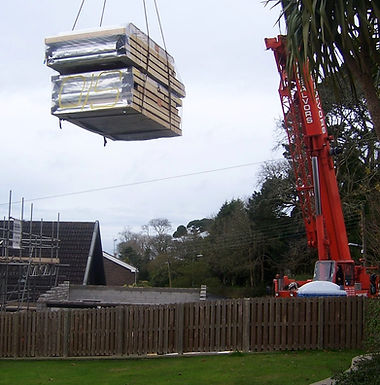
I formed a safety fence around the outriggers of the crane using our Heras fencing, an area that would enclose the counterweight as it swung out towards the road. I wasn't sure if we were required to seek some permission, but at that point we could not take any delay. We hoped that no-one would pick us up on the fact that we hadn't asked for partial closure, or for that matter told the Highways what we were doing. Being at a junction of roads gave more space, and in truth traffic was never held up significantly, and no-one was put in any danger. We all heaved a sigh of relief after it was all over though, and after we had not been challenged about the issue. The truck was completely unloaded to allow it to return to Redruth, and reduce the obstruction in the road, so the first panel was not lifted into position until just after midday.
Progress was good through the afternoon, although when it came to fitting in the West side stairwell panel, which was extremely tight, their propensity to use the sledgehammer as a solution for everything was ably demonstrated, and quite worrying. I soon learnt that another trait, firing multiple nails into panels to join them before being happy they were in the right position, was of equal concern. Problem was, that bashing panels into submission, and then removing the nails with a jemmy because they have to be lifted out again, made a proper mess of the timber and the VCL that had made them a 'closed' panel, and examples of damage could be seen everywhere. I was assured by Charlie that this was all standard practice that the customer doesn't usually see, and it would 'all be right in the end'. Although I was Project Managing, I felt I had to let them get on with it, but I would have a quiet word with Brian, the Frame UK Project Leader.

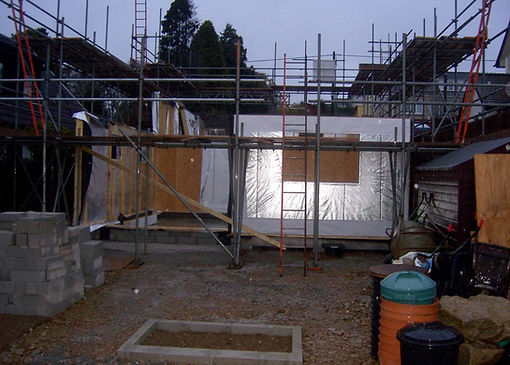
In addition to those unnecessary examples of construction thuggery, a bead of an expanding sealer was applied between each panel, but as it was raining stair-rods by mid afternoon, it was clear that they were just going through the motions, because it was washing off before our eyes. I just hoped that what survived was enough to do the job of making an airtight joint.
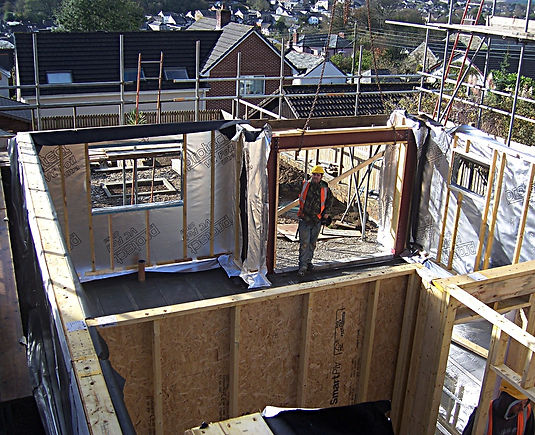

Day 2, and after putting in place all the ground floor walls, the steel goalpost frame for the kitchen folding door set was lifted in and bolted down. With all the steel components, timber interfaces had been fastened on in their plant with shot-fired nails. This would enable connection of other items later, without drilling and therefore weakening the steel. Next in line was the very large H section girder that spanned the whole width of the lower floor, and supported the upper goalpost frame for the lounge folding doors, as well as the lounge floor and partial support of the balcony. I am thankful that qualified Engineers had properly calculated the loading of this aspect of the building design, because it seemed to me that there was an awful lot of weight being supported by two bearings of 150mm x 150mm. With the lower floor walls completed, they began lifting the floor cassettes into position, each one consisting of a number of joists, with flooring attached, and in some instances a temporary joining timber that was removed prior to installing.
In the case of the sections over the kitchen/diner, substantial joist hangers were fastened to timber inset into the steel girder, prior to lowering into position. Each item requiring a lift, be it internal or external wall sections or cassettes, had dedicated one-use lifting straps fitted, which were cut off and discarded when in place.


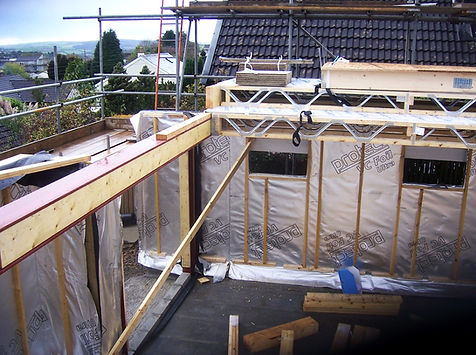


Day 3, and after a fine start, it became very wet, and Charlie was already calling Brian as he had problems.
Brian arrived with a team from the factory, who did not understand what had got wrong, but agreed packing was required to bring the side of the floor sections flush with the outer wall. I think you have to be a certain type of person to be a crane Driver, it would not be for me. Some days, he was only brought into action half a dozen times, but not only was he essential, he was inch perfect with everything, and there was no other way of doing this! By 11.00 all first floor cassettes were in position, the four gaps in the floor covering would then be filled using the squares of pre-cut chipboard also seen in the picture below.
Another full load of panels arrived from the factory, it was difficult to move around now. Included in the delivery was the steel goalpost frame for the lounge doors, these were lifted up, sited, and bolted down to the lower steel girder. Day 3, a Friday, ended much as it started, very wet and cold, with the build pretty much on target, and a break of two days before I would see the merry men again.


I called in on site Saturday morning to find that someone had broken in to the shed and stolen a transformer and extension cables left in there by Charlie. The Policeman seemed to have a suspect in mind, but nothing ever came of the case, I replaced the cable for Charlie.
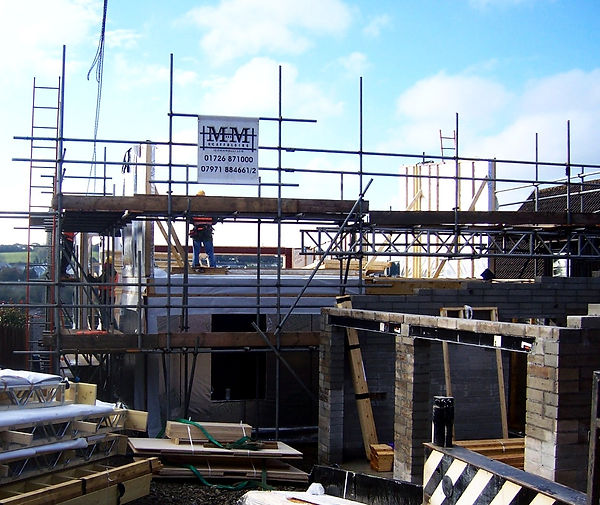
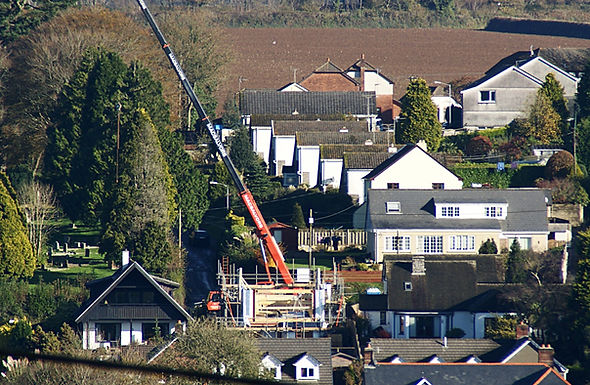
On day 4, Monday 5th November, we were greeted with a better day, and they cracked on with the upstairs wall panels. The picture to the right, through a telephoto lens, is an interesting one from Beacon Road on the South side of the valley.
For most of the day, panels were going in really quite well. A couple of panels though, were not as they should have been. While the other guys carried on, Charlie had called in Brian, and they were in discussion.

In the case of the panel to the right, the lower wall panel should have been produced with a cut back in the top corner to allow the upper panel to fit neatly against the inside wall. It was too late to strip back and remove the lower panel, and so carnage ensued, anyone of a nervous disposition had to look away....Chippy's they were not! The internal panel below which included a doorway, was not high enough and after lining up the top, a gap was left at the bottom. The minor alignment issue of the previous day was also rearing its head, apparently now greater as they built upwards.


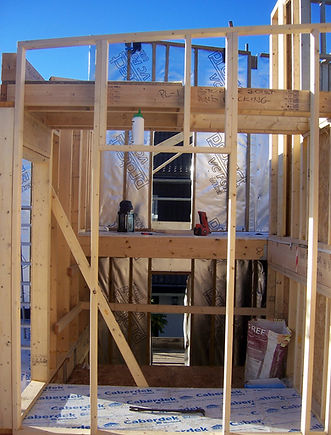
Day 5, and thankfully Brian decided that no further work would be done until all the outstanding issues were addressed. By now I was gaining a great deal of respect for Brian, I considered him an honourable and honest man, and I was extremely glad that I had him as my interface with with both Frame UK and CKR, I would have lost all faith in the project without him there.

Meanwhile, no-one had thought to hold back the next delivery of panels, which would have been sent out to a schedule. Being very large sets of roof cassettes, there was no space for them, and Charlie decided to lay them across the garage wall plates. When Brian saw them he was displeased to put it politely, but Charlie had little choice....this is what happens when schedules hit hold-ups.
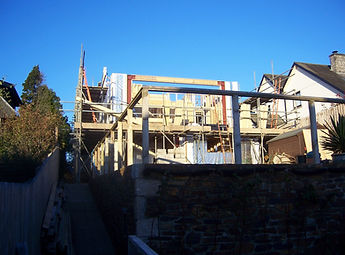

I guessed that whatever needed doing on day 5 to rectify the problems we had was done sufficiently to continue, because day 6 started by loading the roof cassettes on the lower roof. But it didn't take long for them to discover otherwise, mid morning everything was again on hold, and d'boyz were awaiting Brian's arrival once more. He arrived with one of the designers, Jake, who brought his laptop with all the drawings and measurements. No physical progress was achieved for the remainder of the day. They had also still not understood what was causing the lounge to be 'out of square', and cancelled the crane for the following day. A very frustrating day! noted in the diary.
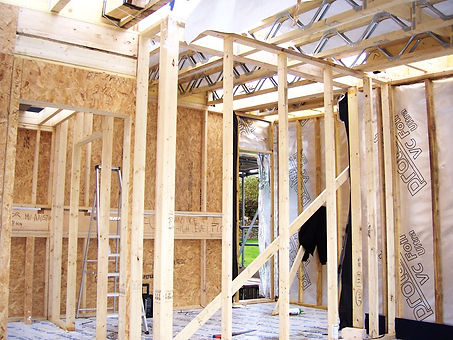
Day 7, and just Me, Brian, Jake, and Ian...one of the erectors on site. Brian eventually concluded that the lounge was out of square due to an accumulation of errors, and he had worked out a plan to correct it. As Ian was the only one there, he set him on to commence with the remedy, but I could see he was very half hearted. I found that he always gave a good impression of someone who simply did not want to be there. The following day (Day 8), all four Erectors were back on site but no crane was required. The day was dedicated to putting everything right and catching up with some of the smaller tasks such as frame ties and fitting battens. Thank God it was Friday again, and a rest from the stress.

All four Erectors back on site Monday 12th for Day 9, no crane needed, as they were still putting things right. A crane was booked for the following day as it was hoped that the upper roof cassettes could be loaded. The last panel to be fitted, the return panel in the centre, which formed the wall of the MHRV loft was made completely the wrong shape by the factory, and rather than wait for another to be made, they used materials on site to make a new one. With all wall panels now fitted, they began laying and screwing down the wall plates.
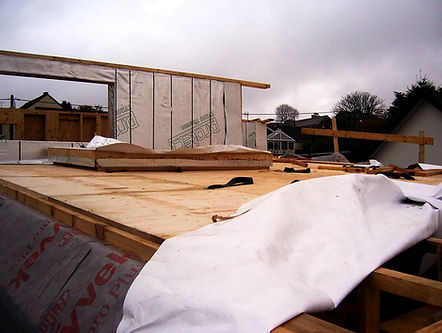


Day 10 started with the arrival of the crane, this time a smaller capacity machine as it it would only need to reach the roof nearest to the road, and the garage. All lifts had been completed by late morning, and by mid afternoon, Crane and Ekki pads had gone from site. A guy called Lee from 'W H Joce' , our chosen contractor for applying the Zinc roof, called to look at the building and discuss what he required of us in terms of how we prepared the roof for him. The roof cassettes were fastened down and the roof was left for the day with only the ply decking to be completed. The following morning Day 11, Colin and Gary arrived to scrape up and remove the quarry waste that had been put down for the crane, leaving the area clean and profiled, he took the waste home for his own yard.
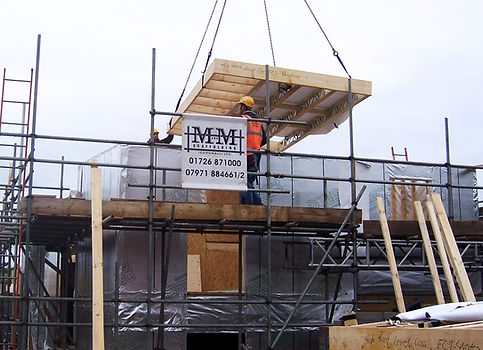
Charlie was taking time off, he said he had things planned as he thought they would have been finished by now. I believe that his relationship with Frame UK was breaking down, he blamed them understandably for the issues that were costing him time to put right, and he said it was unlikely that his contract price would be adjusted to compensate. As I said before this is where this type of relationship falls down badly. Things were bad enough when they were motivated, now they in effect working for nothing it did not bode well. Without their leader things got even worse...really...an overhang of 25mm had been left in the ply on the gutter sides, in case the roofer needed it. When I checked with Lee at WH Joce, he said that he wanted the ply finished flush, so what happened, a circular saw was used to cut the end off, but it was cut back too far. Brian instructed them to remove all the last sheets and fix new ones to the correct length.

Day 12, and M&M arrived to extend scaffolding across the balcony (this could not be done before because of the need to lift in panels and steels), and a single lift around the garage. Only Ian was on site trying unsuccessfully to look busy, and he left early.
Day 13, and no-one from CKR was on site, Brian turned up late morning to 'snag'.......but there was so much wrong, he gave up and went away very unhappy and embarrassed by it all. We had reached another Friday, but the misery would continue.
In Channel 4's Grand Designs, when things go t**s-up, they always play a mournful tune on a harmonica, this was one of those moments.
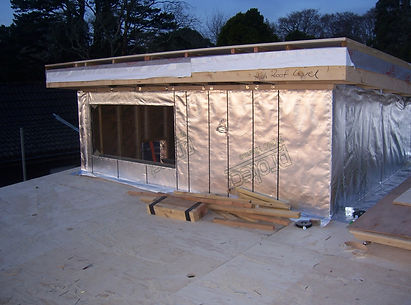
Day 14 and two CKR deputies were on site starting to build the garage roof, using a mixture of pre-constructed ladders and loose posi-joists. After a while I looked up and noticed that a narrow section of ladder was sitting well into the garage which served no purpose at all. I quickly deduced that the solid joists were a wall thickness apart, and in fact should have been either side of the wall to provide fire protection between the porch and the garage. I pointed this out to Ian, who told me that it could only be fitted one way, but agreed that's probably what it was for. In truth I reckon he knew all along, the section had been made in the factory 'wrong handed', but he just couldn't be bothered to say anything about it. At this point I lost it with him....and vented my spleen to Brian, who quickly arranged for a correctly handed replacement to be made and delivered later that day.
Day 15, Brian arrived with Charlie, perhaps because of the 'spleen-venting' yesterday. The garage roof was completed during the day, and for the first time we were in the dry. The whole frame , and especially the flooring, had been soaking wet since the day we started, and it would need a great deal of drying out. My job for the past few days, and a few more to come, was to fit noggins under the joist extensions and barge ladders ,and cut and fix the masterboard soffits, which needed to be ready for the roofers.
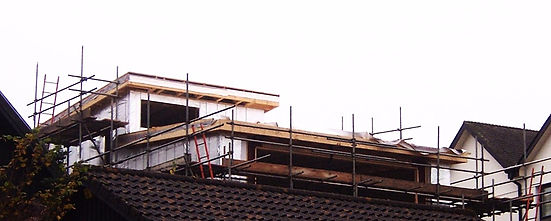
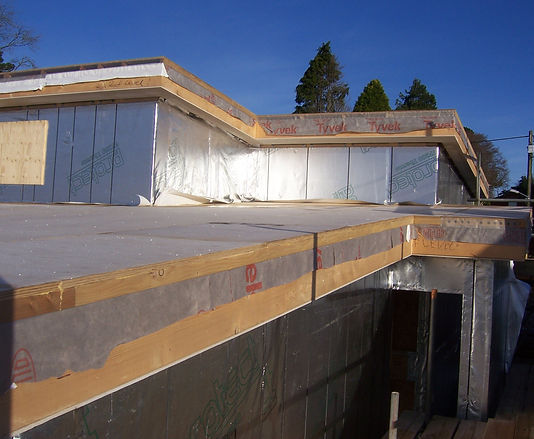
Brian was the only arrival on Day 16, to carry out another 'snagging' visit. I pointed out to him how badly the chipboard flooring had swollen where the small sections had been fitted on site. He promised me that these would be rectified once the windows were in and the building had dried out (a promise he did keep, but the remedy was only partially successful) . I also pointed out a few places where the outer sheathing board appeared to be bowed outwards. He arranged for CKR to visit the next day to carry out the final works on his snagging list. This included repairing a great many holes in the sheathing material inside and outside, with specialised silver tape. This last day with us was particularly wet and violent, we watched from the scaffolding as a tree was blown onto three cars in the 'White House' car park less than a hundred yards away, and I had to take action to stop a sudden downpour flooding the site. A fitting end to a time that had caused us so much grief, and would continue to taunt us with knock-on effects.
Well that was pretty much it as far as Frame were concerned, the next visit was on 3rd December when Brian arrived with our Architect, Chris Wells, to look at snags. This 'post snagging' did throw up a few minor issues, which resulted in a short visit by one of the CKR boys, can't remember who. The handover visit was by Brian alone, I wanted to keep him on board, being the only senior person at Frame I trusted, and duly signed the 'Handover Certificate on December 5th. At this point there were still issues regarding the crane costs and quality of the build.
Finally on 17th Chris arrived with Neil Stevens, the then Operations Director at Frame UK, and Jane Stevens, the Development Manager and wife of Neil. Although Chris did complain about the 'butchery' that we had experienced, by this time I was concerned that Chris was perhaps a little too cosey with Frame UK. I was pointing out a number of places where things were not vertical, and other places out of square, and when you look from the garden you can see very clearly that the problems that halted work for days was never properly sorted out. All of this was basically just dismissed. I'm pretty sure Neil Stevens would have been the sort to convince the Mayor of Pisa that his tower was perfectly within limits! (Yes I know....it was caused by uneven ground compression, just a bit of poetic licence). Chris was pointing out Frames's failings and bad practices, but I don't honestly believe he fought my corner hard enough. What was done was done, and the only thing that could have been given was some compensation. In the end I just wanted Frame UK out my hair for good.
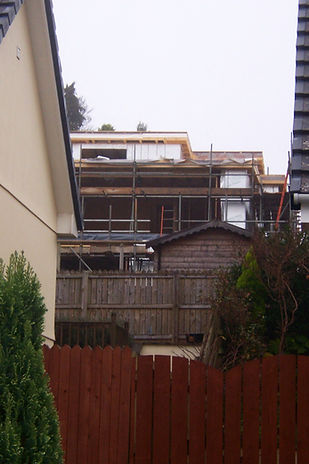
The initial quotation for the timber frame build was around £34k, but with changes to design and increased thermal specification, and the lions share of the larger crane, the total became just short of £44k. In hindsight, after working on the rest of the build with a brilliant Carpenter, I wish I had been confident enough to build the frame on site from scratch. I believe most of the problems we had were caused by the factory making mistakes and out of specification panels, exacerbated by poor quality workmanship on site. I can't say if another supplier would be any better, we'll never know, but I cannot bring myself to recommend Frame UK. My reasons for not building from scratch were chiefly the hope that it reduces the frames exposure to poor weather.....it certainly didn't work out for us, everything got soaked in any case. I'll know what to do next time....if there is one!