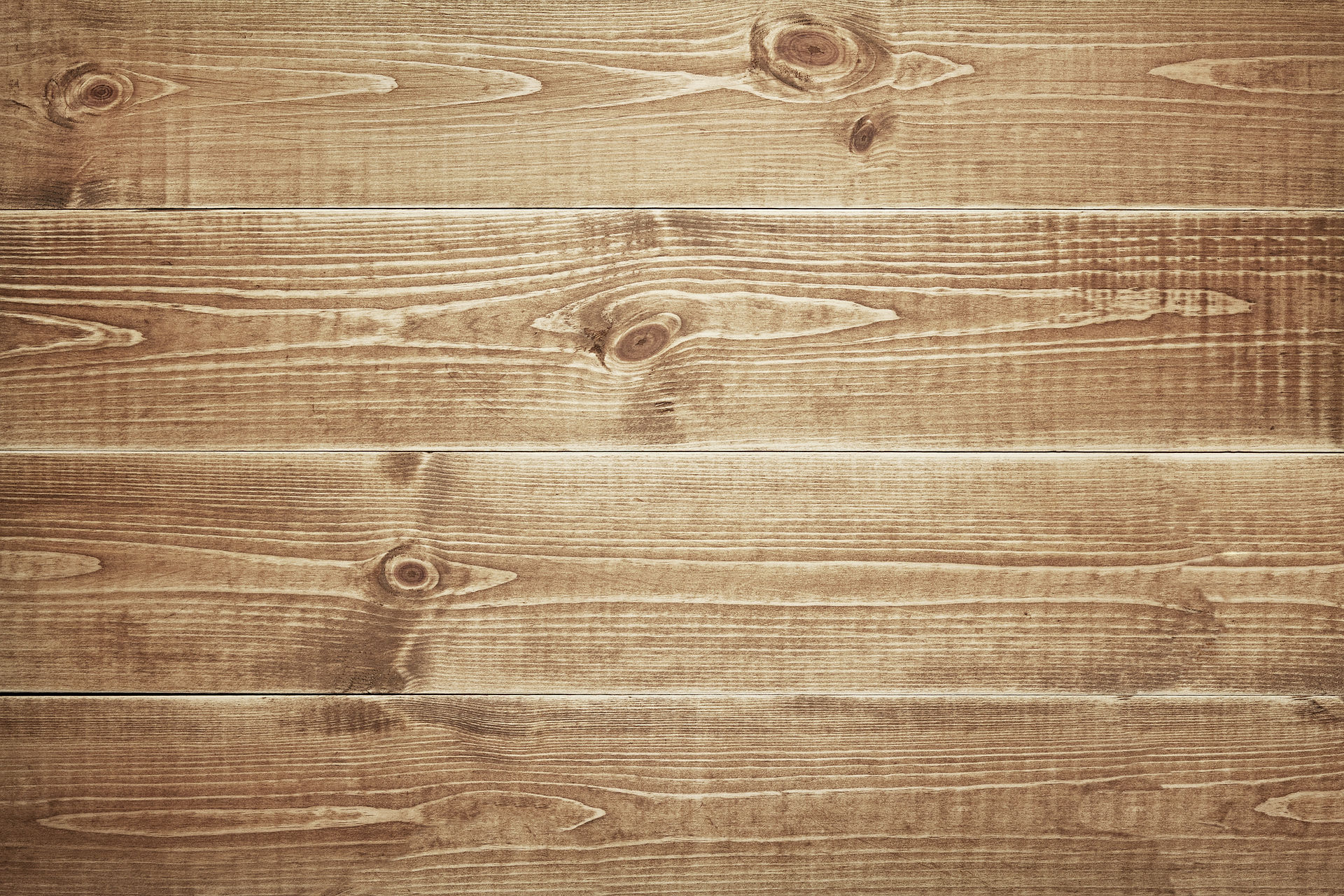
There's something luxurious about ......Underfloor Heating.....
Our last house like the vast majority of water heated homes, had radiators and thermostatic valves. Whilst this does work perfectly satisfactorily, the radiators always seem to be in the way of something, and are a bit of a pain when it comes to decorating. Our valves often failed and had to be replaced, and the pipe connections were visible, quite ugly, and often used to leak because they had been knocked by the vacuum cleaner. Underfloor heating is not new, and there are lots of firms out there willing to sell you the components to do it, or complete packages including design. We had spoken to many people at trade and self-build shows and had firmly decided that we would install underfloor heating throughout. The benefits were clear to us, being clutter free, and the thought of walking on warm floors, especially tiled floors which is where the heating works at its best. A very well insulated house has to be the starting point though, and that is what we planned to have. As the system would be working through a thermal store (hot water tank), another benefit would be the facility to fall back on an immersion heater if the boiler failed. In Arlington we had been without hot water for a week when the combi boiler failed under guarantee, and we were awaiting a spare part. We had also decided to install a hot water loop, which would provide hot water to taps almost instantaneously (avoiding wasteful draw-off), and heat the bathroom and en-suite towel rails.
We then needed to decide what method we were going to use for heating and hot water. We loved the thought of getting sustainable energy from non-fossil sources, and were very keen to investigate the possibility of a heat pump system, air or ground source. Despite grants or pay-back schemes, the equipment is very expensive, and in the case of ground source, the bore hole would have been around £7k on its own (not having enough garden to lay a large loop underground). Some of the justifications I read were so unbelievably rose tinted too, citing the high cost of a boiler and annual servicing, when compared to the heat pump kit, these factors are minimal. The absolute deal breaker though, was the fact that the hot water temperatures derived from these systems is good enough for underfloor heating, but not really good enough for domestic hot water. As a result therefore, you have to boost water temperature using some other method, or use another method completely for DHW. A non-biased expert at the Self Build Centre in Swindon said to me, "if your house is in a town with a piped supply of natural gas, it is, I am sad to say, a no-brainer". So....a gas boiler it was going to be.
Once we had a set of building regulation plans, we sent out requests to the two companies we had shortlisted, to provide a quotation for a complete design and supply package. We had also asked our Self-Build Rep. Greg Blee to see what prices he could achieve. We had researched a great deal over the months, and although not the cheapest of the quotes, Nu-Heat was standing out as the best option, and seemed to have a great reputation. Greg got a slightly better price on the basis of volume of business with Jewsons (since we started working with Greg, Wolseley (Build Centre) had been taken over by Jewson). We placed an order for the system, including a 210L Energymaster Thermal Store, and an Aquastar hot water loop.

On 5th October 2012 I drove up to Honiton to the training centre at Nu-Heat, for a one day underfloor heating course. I didn't intend to install the heating system myself, but I did want to know how it should be done, and understand how it all worked....it was well worth doing.
To enable Nu-Heat to draw the detailed plans for the system, Frame UK sent the floor and joist plans electronically. The schematics plans and diagrams they supplied for both the plumbing and electrical systems were superb, great detail and clarity. All the components arrived on Monday 4th February 2013, and by the following weekend I had fitted the 'Clippaplates' ready for our Plumber Rob Button, who would be arriving with us on the 25th.
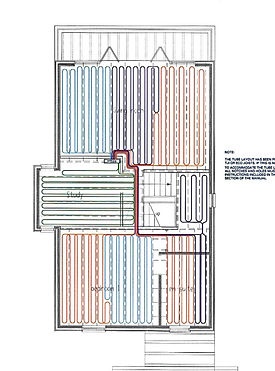
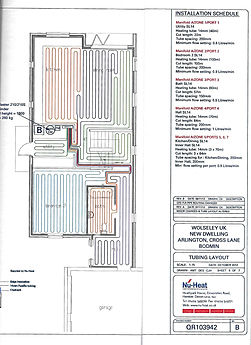

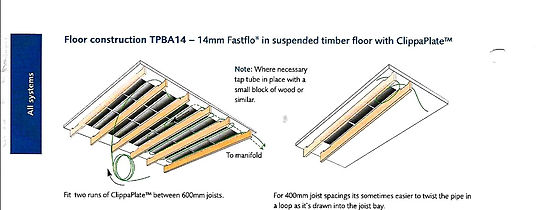

For each of the loops, a corresponding coil of pipe had been provided, and Rob and his mate Dave's first job (Dave only came along when needed to help with the loops) when they arrived was to install the upstairs manifold in the study, and fit the pipe runs into the ceiling Clippaplates. Their technique was improving as they went on, and they had finished this within two days, it had been straightforward, but quite difficult on their necks working upwards, and threading the pipe through the joists at the end of each run. Rob went on to install H&C pipework for the upper floor. They returned on 4th March to lay the ground floor pipes in preparation for the screed. This involved laying rows of plastic 'Cliptrack' using plastic staples pushed into the insulation, surprisingly quite secure. Using the plans supplied, the roll of pipe was then walked around, clipping the pipe into place as they went, with the return loop clipped in with the same staples. This was much easier , and they had it all done, and other work, before the end of the day. The lower floor manifold was fitted and all the pipes were connected and filled with water. The gauge on the manifold registered 2 Bar, the system was left under pressure. I would be watching this closely, especially during the day when Lidstones were on site screeding, as a pressure drop would indicate damaged pipe. Thankfully it survived that day, despite quite a lot of punishment.

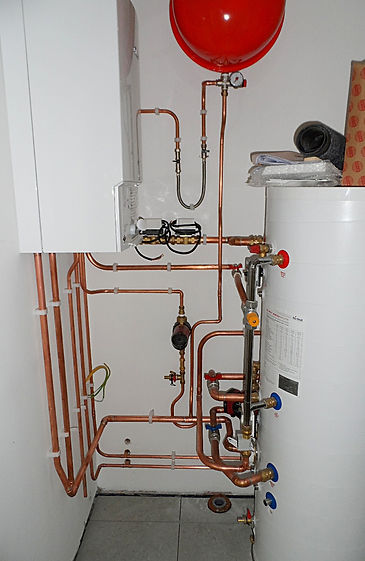



Rob was back on site 14th April, and after getting the en-suite fitted out for our impending occupation, he began by installing the boiler and flue, and the myriad of pipes and components in the utility room. Rob preferred to work in copper, and I was happy to let him. His work was superb, neat and methodical. We purchased the Worcester Greenstar 18i condensing system boiler from Jewsons. At a capacity of 18 Kw (60,000 btu) it was more than the 14Kw minimum output recommended by Nu-Heat. The Tilers had not reached the utility at this point, and we did not want to hold up Rob, so the thermal store was positioned, connected up and filled. The Tilers eventually had to cut the tiles around the tank, no big deal as it was inside the airing cupboard.....still did a very neat job though!
The Electricians were now able to connect everything up. The system included supply of all junction boxes and control boxes, and excellent detailed schematic wiring diagrams. We had chosen digital thermostats for each room, and these were all wired back to the controller. We could have had a central control box but felt that the cost did not provide a significant advantage.

On 26th April, Rob had finished everything and we had a hot water supply, albeit from the immersion heater......but that was fine, it meant we could move in to the bedroom and en-suite. We moved in on 27th April, and enjoyed our first really good shower in 7 months......and a great nights sleep! The gas wasn't connected until 14th May, after which Rob came in and fired up the boiler and got us working fully.
Three and a half years later, we are very pleased with the system, and the control of it. With underfloor heating, the lower level heat takes time to penetrate the floor, so you do not turn it on and off as you do with heaters. You decide when you need it, and leave it on for the winter months until you feel you don't need it. Having said that, as each room has its own electronic thermostat, you can leave it turned on, and when the weather warms up it just won't call for heat! Solar gain, even in the winter, certainly reduces the need for heat in a house like this. A sunny day even if cold will, we have found, warm up the house so that the heating is not brought in at all during the evening. With the addition of the MVHR, we have the benefit of retaining much of that warmth whilst still being properly ventilated.
We have three variations of floor coverings, tile, engineered oak, and carpet. The most noticeable heat is from the tiled areas, there is something quite luxurious about walking on a warm tiled floor....perhaps you can imagine yourself being a Roman walking around on your hypocaust! You don't notice it so much in the wood covered areas because wood is warmer to the touch in any case, and the same goes for the bedrooms and study which are carpeted. However the roomstat gives evidence that it is working. The heating is apparently least efficient under carpet, so you have to limit the total 'tog value' of underlay and carpet to 2.5 tog. We had no problem in achieving this with 'Duralay Treadmore' and a very good quality 40 oz/sq.yd. 80% wool carpet.
The DHW system also works well, supplying endless hot water to the showers. The hot loop supplies instant hot water, we have timed ours to operate at the times we expect to use it, but you can leave it on all day if required. The water in the thermal store is for the heating only, it is quite hot (65 -70 degrees C), and on its passage into the underfloor pipes, cold water is added to reduce the temperature to around 50 degrees.. In the case of domestic hot water, cold mains is fed into a stainless steel heat exchanger within the tank, which quickly heats it up to around 43 degrees before feeding to taps and showers. When hot water is demanded, a flow switch starts the shunt pump fitted on the side of the tank, which cycles hot tank water through the tank side of the heat exchanger. If the temperature of the tank drops below a lower set level, the boiler then starts and runs until the tank temperature reaches the upper set level of around 70 degrees. Because of this, the boiler runs for longer more efficient periods and prevents problems associated with 'cycling'.
We have had one issue with this system, the flow switch failed three times, and each time a replacement was quickly sent FOC. However the third time it caused a shunt pump failure. Apparently a new pump model had been fitted to our system, and they had subsequently found that with this new type, the flow switch required operation through a relay...but ours had not been supplied with a relay. Without the relay, flow switches were failing. The penny finally dropped with them, when they mentioned the relay, which of course we didn't have. On this last occasion, Nu-Heat supplied the new switch, the relay and enclosure, and paid for the new pump, even though the system was out of guarantee. This was of course only fair, and there was no resistance from them to doing the 'right thing'.
I would certainly recommend Nu-Heat to anyone considering underfloor heating!