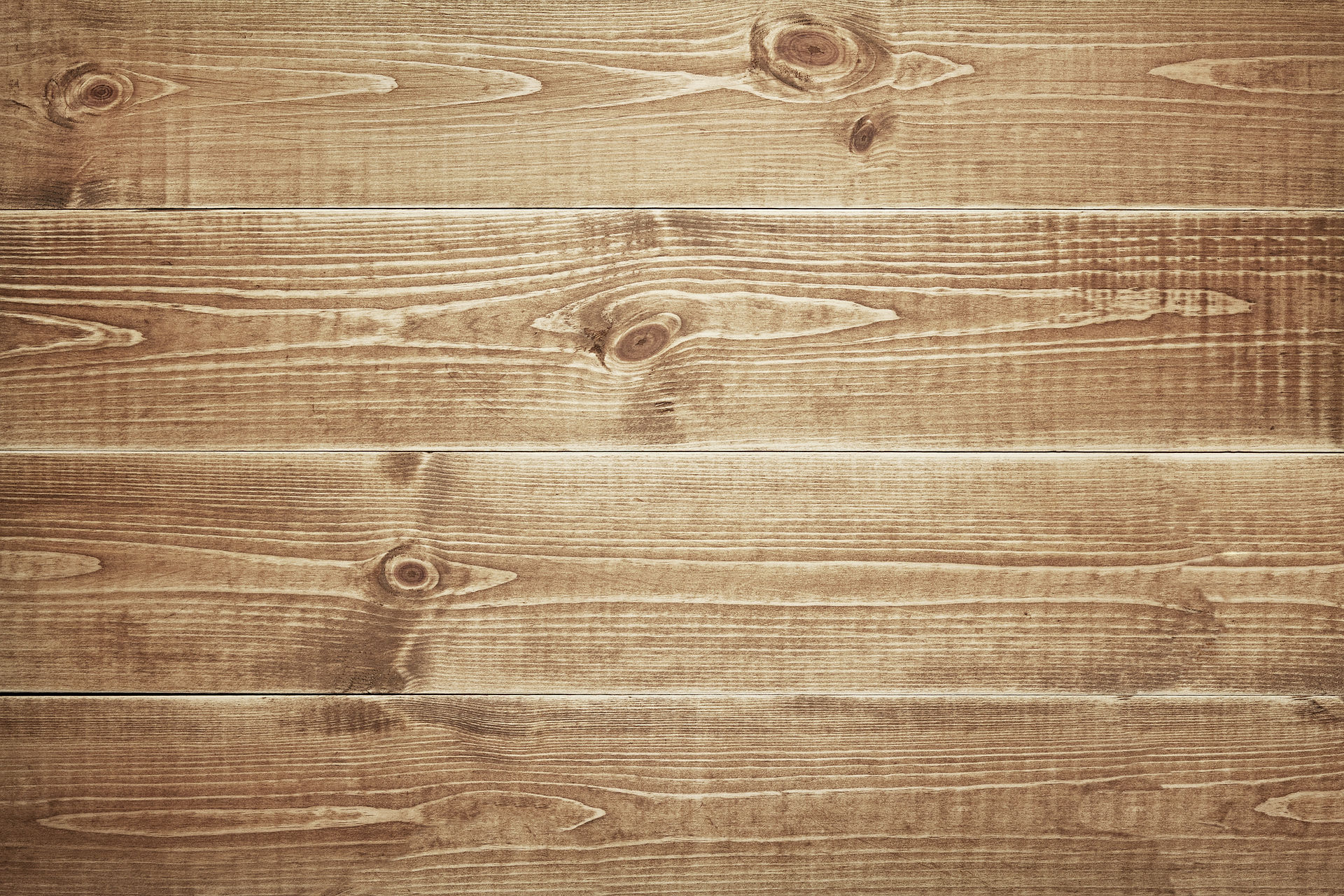
The 'nice bits' ........... Second Fix
For a while, first and second fix tasks were by necessity being worked on in tandem, but I guess you could say second fix started with the arrival of the Tilers, Simon Taylor and his working partner Craig Shaw (CIS Tiling), on 25th March. Over the next 4 days they tiled both the walls and the floor of the en-suite. It was interesting to see how they thought everything through before they even laid one tile, planning every start and finish point, and every corner. As the floor was chipboard suspended over joists, consideration of floor movement and therefore cracking was very important. Simons solution for this was using 'Schluter Ditra', a single sheet of which is stuck to the floor (which he did a couple of days before). The square recesses in the sheet are tapered outwards so that when tile adhesive is applied, it 'keys' itself in to the sheet. Flexible adhesive and grout is used throughout, and nearly four years later, it is still perfect. We chose 'Marazzi Zenith' 760mm x 250mm beige tiles in plain and ripple effect, two rows of ripple at eye height and one row three up from the floor. The floor tiles were a floor quality version of the plain wall tiles.
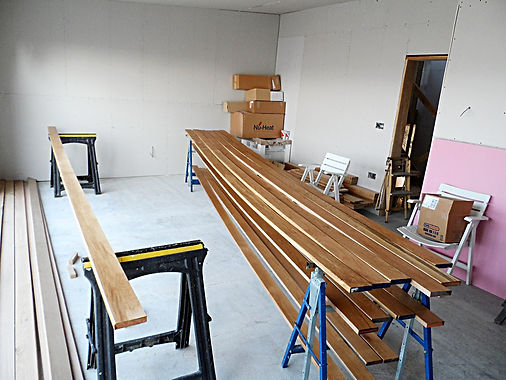


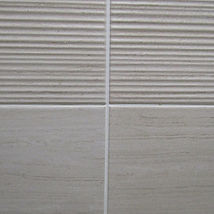
The Oak skirting and architraves from Charlestown Joinery arrived on March 27th. We took the long lengths upstairs to the lounge, and Elaine started to give all the faces that would be exposed, two coats of 'Osmo Polyx Hardwax Oil'. As soon as these were dry, Clint could start on the bedroom.
On April 9th, 'In Steel' arrived with the polished stainless steel balcony components that they had fabricated at their works in Redruth. This was not the first visit with the balcony. A couple of weeks earlier, their whole team had turned up with the balcony rail and uprights, in one 6.5 metre long piece, on a wagon. As soon as I saw it, I could see it was wrong. They had made it the same height all around, whereas the plan was for two 1.8 metre raised sections at either side with obscure glass. The plan that they provided me showed it clearly, so it is beyond me how it could have been made that way! What is more, the 10mm toughened glass was also made, I still have the two incorrect ends in my garage Anyway second time lucky, everything was right, and beautifully finished. The support brackets were bolted on to the balcony walls, the copings were fastened down and sealed to the brackets. The rail was positioned, this time in three sections, and fastened to the brackets.


The two joins were then expertly welded and polished on site, and the glass fitted. Although they did make an embarrassing foul-up, the loss was theirs. We were and still are very pleased with the result.

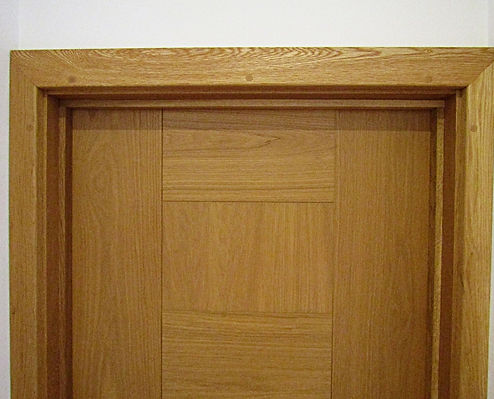
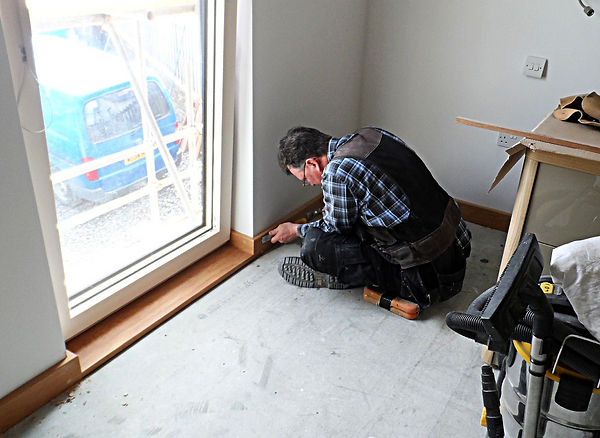
With the skirtings and architraves coated and the doors delivered, Clinton was able to move on with the master bedroom second fix. The 'chunky' oak window sill board and skirting were designed to form a clean line to continue the carpert edge, and all were drilled, screwed and plugged. In the picture left Clint is carefully trimming back the plugs level, time consuming work, but the appearance is worth the effort. Just a dab of Polyx Oil afterwards, and it all blended in beautifully.

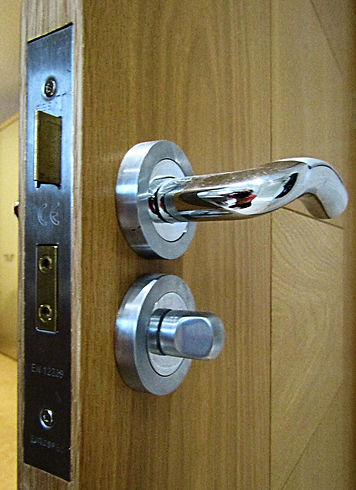
We shopped around for doors, but in the end found exactly what we needed through Jewsons. The 'Jeld-Wen Joinery' oak veneered engineered door in a design called 'Cube' gave us the look that perfectly complimented the house and the squared-off style we had used for skirtings and architraves. These came in a plain panelled door, and one with three frosted glass panels....we had 4 of each style. The stainless steel 'on-rose' door furniture was from 'Fortessa' , in the 'Milan' style. These handles look beautiful, and feel comfortably solid and expensive, but we actually picked them up for around £14 a set online from alldoorhandles.com. Good quality stainless steel hinges, locks and catches were used to complete the high specification appearance.
Our Tilers, Simon and Craig returned to site on April 11th, and would now stay until all work was completed. We were concerned whether or not the floor was dry enough, as it was only a month to the day since it had been laid, and I had read that floors can lift because that causes adhesion problems and chemical reactions. Anyway, Simon checked the floor with a moisture meter, and it was fine, the additive had done its job. They started in the bathroom, where we had chosen simpler 'Siena Beige' 330mm x 250mm tiles, with contrasting stone mosaic strips. We had envisaged spreading these mosaics randomly, but Simon and Craig convinced us they would look better in solid floor to ceiling strips. We agreed, and I have to say it was the right thing to do, as we were very pleased with the result. After the walls, they continued by laying the floor using 'Venus Tyrrhenia White' modular pattern tiles. These came in boxed sets of a variety of sizes, and would be used for the floor throughout the hall passage and bathroom. Though these tiles look like marbled stone, they are in fact ceramic tiles, and are therefore more serviceable.



Having completed tiling the Hall, passage and bathroom, the Tilers moved on to lay tiles in the kitchen dining room, utility and stairwell, using 600 x 600 'Gemini Hillock' Grey tiles. They also confirmed that Lidstones had laid a good and level floor, essential with such large tiles.

We had ordered our 'Nolte Evona' bedroom furniture back in January, all of it was freestanding rather than fitted, but when it came to calling for its delivery, it would arrive mainly flat-packed and then be erected by a team of installers. They arrived as requested on April 16th, that was a very busy day as I recall, with 12 of us on site including me. The Tilers were busy laying tiles in the hall and bathroom, and therefore the delivery of furniture had to be made directly through both bedroom windows. The upstairs items were first lifted up on to the scaffolding, then passed through the window, in fact this made it easier. We had chosen a glossy coffee coloured finish (sahara) with woodgrain frames for upstairs, and white finish with woodgrain downstairs. They were put together very efficiciently, and they were out of our hair in no time. We were very pleased with both the wardrobes and chests, all very substantial, well made and surprisingly heavy. The wardrobes were laid on a sheet of OSB cut to the size of the base to give clearance for the doors to open when the carpet was fitted.
Our plumber Rob, had fitted the shower screens and sanitary ware in our en-suite, and connected up the sink, toilet cistern, and shower mixer. The wall hung basin unit, cistern unit and tall cupboard were all from Jewsons, a brand called 'Shades' and the woodgrain pattern was called 'Driftwood'. We had three basin units delivered, as on the first two occasions they had been damaged in transit. The first replacement unit arrived from Jewsons on top of a load of other goods, and it had been strapped down hard, as soon as I saw the distorted box it had arrived in, I knew instinctively that it would be damaged because they had been strapping over a very weak point, and it was! The third unit eventually arrived intact. All the shower and tap fittings for both bathrooms was made by 'Grohe', we love the design of their products, and the rock solid quality that you would expect from a German maker.
To enable us to 'camp' in an unfinished kitchen, or at least feed ourselves and wash dishes, Clint was now fitting some plain white units and a grey worktop in the utility room, and Rob was fitting a sink and taps. We were also able to connect up both the washing machine and tumble dryer. (The tiles came much later).
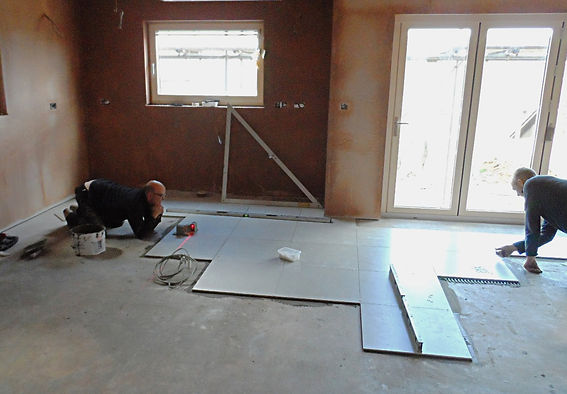




The Electricians came back to fit lighting, sockets and switches where needed as areas were being finished. We did not want fancy fittings, and chose the high quality and simplicity of MK Logic Plus. We chose mainly down-lighters for every room, and bought 63 'Aurora' fire rated fittings in three types, swiveling, fixed and enclosed IP65 for the bathrooms. These fittings all use GU10 lamps, and we fitted LED throughout, warm white, cool white, and daylight depending where they were fitted. Charlie had carefully charted where the ends of ceiling light wiring was waiting to be found, and where he would cut holes in the ceiling, in all areas except the lounge which he left to A.N.other! Until he got to the lounge, everything worked out perfectly....and then it happened, the holes were cut and he found in two cases that a joist was in the way! Now Charlie is a smashing bloke, he takes his job very seriously, and after this, he couldn't face me. I knew who was at fault, I smiled, told him to get on with it, and made the ceiling repairs....no big deal! It's good to have such conscientious people doing work for you.

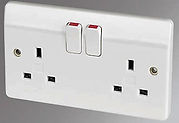
The bedroom carpet was fitted now, and finally we had sufficient 'life support' to allow us to move in, which we did on Saturday 27th April 2013.
Our next door neighbour Steve Evans had kindly offered not only to help us move our belongings from the rented bungalow, but provided a van to do it, we were very grateful for that. It took three trips, and it wasn't very far to go, but upon our return after the second trip, Elaine told me that we had a hot water leak! I knew it wasn't the heating because that was not turned on. It was leaking along the ceiling of the downstairs bedroom, and down the wall, so I pulled down a couple of the down-lighters and shone a torch into the void. I knew where the pipes were routed, and luckily despite the insulation, it was clear where the water was dripping from. I managed to reach in enough to pull the insulation aside, and measured its location from each wall. Having turned off the water, I pulled back the carpet in the bedroom above, and marked where it was. I could see from below that the 22mm pipe was situated centrally between the joists, which meant that I could cut a hatch into the floor, that would be in the space between 'clippaplates' and in doing so i would not endanger the underfloor heating pipes. Upon carefully cutting out a panel, I found that a 90 degree elbow on the pipe was the cause of the leak. Rob arrived the following day to replace it, he said it was the first one he had ever known fail, and in fact you could see solder all around the join. It hadn't caused much damage thankfully, but took a couple of weeks to dry out completely.
Later that day, my Best man Tony Lewis came to stay on his annual pilgrimage to Obby 'Oss, we went to Wetherspoons for something to eat and a drink...or two. The following morning we were having breakfast, he went to to the bathroom and found water gushing everywhere. Ecky Thump!!!! The toilet cistern, which is a plastic container with all the floats and valves inside, had come away from the wall, still inside the unit, but was spilling the water it was continuously calling for. We were all paddling by then, but quickly turned the water off and got the wet and dry cylinder vacuum to suck up the water. The heads of the screws that Rob had used to fasten the cistern to the wall weren't large enough, with the weight of water inside, the plastic fastening lug had gradually eased itself over the screwhead, and the cistern dropped down. I shudder to think what we would have faced if we were out at the time, and I took measures to ensure that it couldn't be repeated. Hopefully that was the end of the nasty surprises.........
In between the various tasks helping and organising, I had continued cleaning up and painting walls whenever I could get to them. We eventually carried out all the decoration ourselves, inside and out. The lounge had been given a mist-coat of McPhersons white, followed by two coats of Dulux 'Cotton White', the colour we used throughout. Clint and I moved in to put the floor down. We had chosen an engineered oak 'Tuscan' flooring from Jewsons, over a good quality foam underlay, and it was very easy to lay. It took us a little over a day to get it all done. Clint then went on to fit the skirting boards, and build a raised threshold for the door, which was installed just below the top of the bottom door track and level with the top of the skirting. This looks great and the vertical blinds that are now installed sit nicely above it. When we pull the door back, this becomes less of of a trip hazard than the rail on its own would present.


All ceilings had been plastered and painted by 13th May, when Ben arrived from Villavent to commission the MVHR system. This involved fitting all the ventilation duct terminals in the ceilings, the external inlet and outlet louvres, and starting the fan unit. He then used measuring equipment to check and adjust for the correct flow rates and temperatures for each of the terminals or 'registers' as they to refer to them.
The kitchen units had been delivered and stacked up in the kitchen. We had chosen a local kitchen outlet Miles McQuillen Kitchen Studio, mainly because we had used Miles before and were very pleased with him, the quality of the kitchens, and the great service he gave us. We chose a style that was fairly 'low key' because we felt that would better suit the large open plan kitchen dining area that we planned. Miles supplied units from 'JJO' Colonial Avola range in a mixture of white and grey finishes


We had shared our thoughts and ideas with Miles, and his first attempt at a plan for us quite closely reflected what we desired. With a large kitchen like this, the possibilities are so much more varied than a small kitchen which might be much more restrictive. After 'kicking' around his ideas and a few more of our own for a while, he produced the plan to the right here which is exactly what we built.
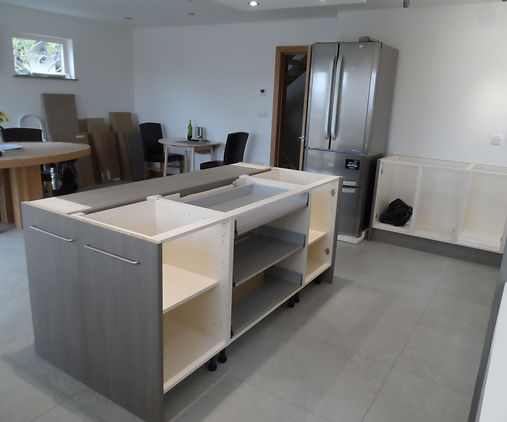

The design called for quite a lot of fabrication using panels cut down to size and shape, the island in particular. The trim panels that were fitted above and below the wall units, and formed the ends, required a great deal of skill to cut precisely and cleanly without chips! Clinton was particularly good at this, and with my basic skills used to make the units from flat-packs and his superior carpentry skills to create the bespoke finishes, we had the kitchen completed by May 30th. That same day, Alex from 'Everything Stone' in Par, arrived to make the templates for the worktops. The 'Best Cirrus' extract unit was properly fitted now, a bit of extravagance, but it is very smart, powerful, and completely unobtrusive.

On June 3rd, Charlestown Joinery delivered the Oak stair sections, with all the associated newel posts and trims, in addition to an Oak door frame for the study cupboard, which we had decided would have sliding doors. He started with the lowest flight down to the kitchen, and quickly found that they were not correct, with the treads level, the riser for the first step was 15-20mm more. It doesn't sound much, but it is amazing how you feel the difference when you step down. The problem was that they were keen to get started making them up, and against our advice took measurements from the insulation before the screed and tile. Clint left them and carried on with the second and third flights, which were correct. John from Charlestown was called in, he decided that a new flight would have to be made, and measured up for them. The following day the offending steps were taken away in handcuffs. Whilst we were waiting for their return, Clinton fitted a sub-floor and frame for the study cupboard, then went into the lounge to build a frame around the gas fire to support the slate hearth.

On Tuesday 11th, John returned with the new flight of stairs, Clint was finishing the skirtings and door frame in the study. The following day he started fitting the new section of stairs, and had completed them including rails, trims, and stainless steel glass support clamps, on the 14th June. We then laid the 'Tuscan' wood flooring on all three 'landings'. The previous day when almost finished, John had called in to make templates for the glass stair panels.

On Thursday 20th, doors arrived for both the under-stair store and Study cupboard. Having no loft to squirrel away any bits and pieces we might want to store, it was important that we had some storage somewhere. Early in the design we noted the area under the first landing would provide an easily accessible space, and so it was, the space has been invaluable. Clint had to cut down a standard door in this case. The sliding study doors were bought online from B&Q, and once the packaging was removed it became clear that the rails were too short, and not the length written on the order. We asked for the replacements straight away, but didn't receive them for 14 days. When we did eventually get them they were very simple to fit. The glossy black glass and aluminium trims contrasted beautifully with the oak framing.
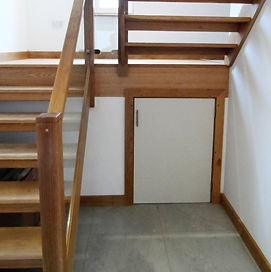
Alex arrived with our kitchen work-tops on 27th. We had chosen 'Diresco Premium Mistral Grey Anticato', a product we had seen in a kitchen display at Miles McQuillens showroom. It is an extremely strong engineered stone product made from high strength resins, with granite and quartz granules. Holes had been cut in it for the hob, underhung sink and tap, pull up socket, and waste disposal switch. The surface by sink had been ground to produce a draining area. We had also ordered splashbacks and window sills in the same material, all of which Alex fitted.

Before he left, he went up into the lounge and made a template for the gas fire hearth. The main lighting in the kitchen area was from 'Saxby' lighting tracks with 'bullet' fittings housing cool white LED'S, which were fitted whilst we were putting the kitchen units together. The following day Charlie called to connect up all the appliances, and everything was done! Now as you can imagine at this stage, a certain member of the household who had been dreaming of this moment for years, and who had been carefully choosing appliances, fittings and furnishings, was primed and ready. It didn't take long therefore to have all the blinds and curtains up, and ornaments and catering ephemera out on display. We were both well pleased with how it had all come together. It was 29th June, three months since we had moved in,


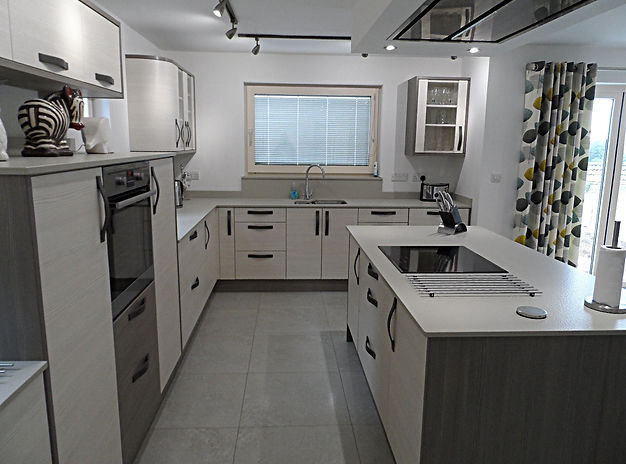
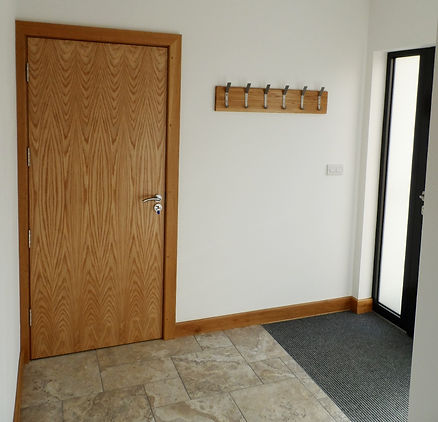
The door into the garage required a 60 minute fire door, and Jeld-Wen did not make one in the Cube pattern we had elsewhere, so our best option was a plain oak grained door, simple you would think. I ordered one from Jewson, but when it arrived, it was sliding around in the back of the lorry and it was scratched to hell, and 'protected' (ha) by a thin sheet of polythene that was in tatters. I refused to off-load it, I could not believe the mentality of anyone loading it that way. On top of that, it was hideous, so I didn't ask for a replacement. I found what I needed from www.doorstoresonline.co.uk, and it arrived on 28th June......damaged!!!! A 2'8" 60 min fire door is very very heavy, and unbelievably it had been delivered in my absence by TNT with very little protection. When I rang the company they were amazed that TNT had delivered it, as they stipulate a two man lift and TNT are always 'Lone Rangers'. Anyway, possibly because someone was struggling with it alone, it had massive dents in it, so it had to go back. An undamaged item arrived several days later on 11th July, and with my help, thus avoiding a hernia, Clint fitted it with four good quality ball bearing stainless steel hinges. (they came in pairs so we thought we'd use all four rather than just three).
Elaine had given the stairs and rails two coats of Polyx Oil by the time the glass was delivered by Charlestown Joinery. The main panels were quite heavy, so it was a two man job which Clint and I managed without mishap. We loved the whole Oak and glass combination, and it has been very easy to keep clean.

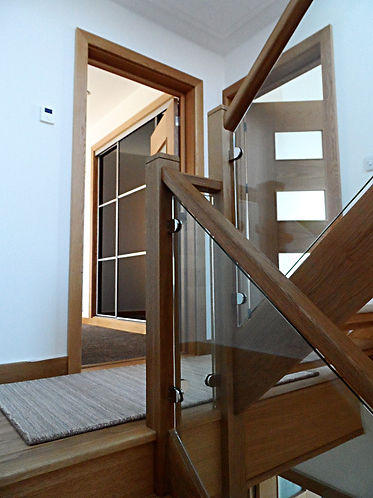

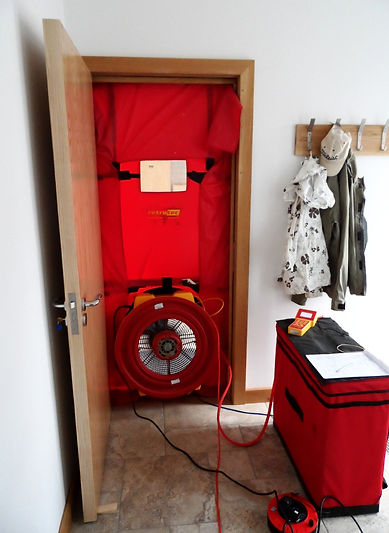
On 18th July, Clinton had finished. I would be calling on him at some point later to put together an airing cupboard, but he had been here with us pretty much most working days since the beginning of the year. We enjoyed our banter and intelligent conversation, he had become a friend and it was with a tinge of sadness that we watched him drive away that day.
On 26th July, LABC (building regs. arm of Cornwall Council) arrived to carry out the obligatory Air Tightness and SAP test for the princely sum of £300. We were expecting good results, best practice being 3 and normal being 9. Our result of 5.13 was quite good, but I know why it wasn't better. All the down-lighters have to have apertures in the tops of their 'cans' or containers, to allow the lamp heat to dissipate, and lined with intumescent material that expands in the event of a fire.

Although the LED lamps we used give off very little heat, that is the design which should not be interfered with. When the test was in progress the air passing through the adjustable down-lighters was like a gale, so clearly they reduce the air tightness, and subsequently thermal efficiency. Although it is logical that this would happen when you cut holes in the ceiling, I did not give it a thought, read about it, or have anyone mention the possibility. If by mentioning it here better prepares anyone reading this who might be undertaking a build, then I recommend examining lighting possibilities that avoid this.
Clinton joined us again in September for a couple of days, to build the airing cupboard in the utility, enclosing all the heating equipment behind doors. Over the next few days we primed, undercoated and painted frames and doors in satincoat.


One thing I find amazing now that I look back on it, is that the waste from this build was so minimal, we never had a skip. I guess some of that will come from the fact that I was Project Managing, and it was our money, so we kept a close control of materials ordered. All the timber off-cuts and non-returnable pallets were taken just around the corner to Dave Worden to use in his log burner, and any waste OSB or ply off-cuts we could not recycle, went to the wood skip at Lanivet amenity site. The few blocks and part blocks that remained were utilised in the garden walls, or at worst hardcore. Off-cuts of plasterboard, also went to Lanivet into a special skip, but since that time they have started charging quite a lot for this. Beyond that, all cardboard was recycled, and anything else was bagged and went to Lanivet. It wasn't significant because it all went in the boot of my saloon car at intervals during the build.
We bought a first aid kit to keep on site, it was opened only a couple of times for the inevitable nicked finger.....so I am pleased to say that "no animals or humans were harmed in the production of this house".
As far as second fix was concerned, it was all done and dusted. To say we were pleased with what we had achieved would be an understatement. We'd had a few problems on the way, a lot of it totally avoidable, but as one old hand told Shane once........"building is just one long problem solving exercise"....and that is the truth.